Porosity in Welding: Identifying Common Issues and Implementing Ideal Practices for Avoidance
Porosity in welding is a pervasive concern that usually goes unnoticed until it creates significant problems with the honesty of welds. This usual defect can endanger the stamina and toughness of bonded frameworks, presenting safety and security threats and resulting in pricey rework. By recognizing the source of porosity and carrying out efficient avoidance strategies, welders can significantly enhance the quality and reliability of their welds. In this discussion, we will check out the vital aspects adding to porosity formation, examine its destructive impacts on weld performance, and go over the very best practices that can be taken on to reduce porosity incident in welding processes.
Usual Reasons For Porosity
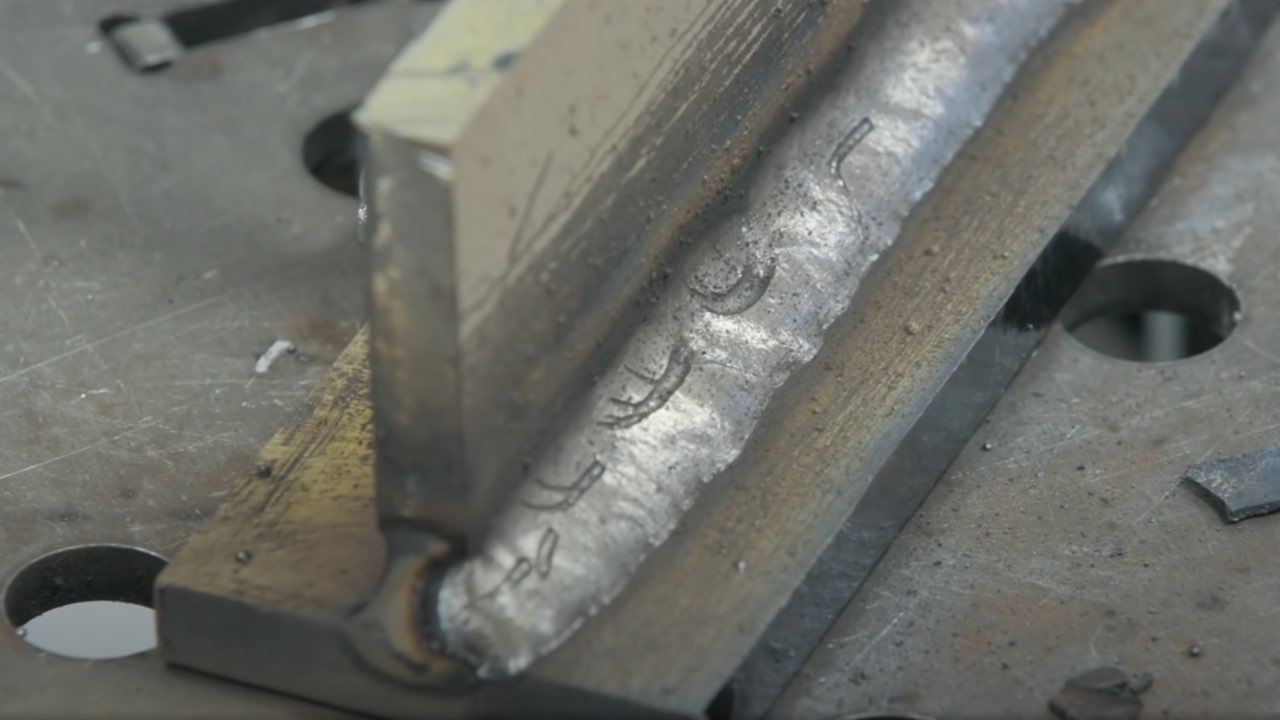
Utilizing dirty or damp filler materials can present impurities into the weld, contributing to porosity problems. To mitigate these usual reasons of porosity, thorough cleaning of base metals, proper securing gas choice, and adherence to optimal welding parameters are essential techniques in attaining high-quality, porosity-free welds.
Influence of Porosity on Weld Quality

The visibility of porosity in welding can substantially compromise the architectural honesty and mechanical homes of welded joints. Porosity creates spaces within the weld metal, compromising its general strength and load-bearing capacity.
One of the key effects of porosity is a decline in the weld's ductility and toughness. Welds with high porosity degrees often tend to display lower impact stamina and decreased capacity to flaw plastically before fracturing. This can be especially worrying in applications where the bonded parts are subjected to vibrant or cyclic loading conditions. Moreover, porosity can impede the weld's capability to properly transfer pressures, leading to premature weld failure and potential safety and security risks in important visite site frameworks.
Finest Practices for Porosity Prevention
To enhance the structural honesty and high quality of bonded joints, what specific steps can be executed to decrease the occurrence of porosity during the welding process? Using the proper welding method for the certain material being welded, such as changing the welding angle and gun setting, can further stop porosity. Normal inspection of welds and instant remediation of any type of issues identified during the welding procedure go right here are crucial practices to avoid porosity and generate premium welds.
Value of Proper Welding Methods
Carrying out correct welding methods is vital in ensuring the structural honesty and quality of bonded joints, building on the foundation of reliable porosity avoidance procedures. Welding methods directly affect the general toughness and sturdiness of the bonded framework. One key facet of appropriate welding techniques is maintaining the you could try these out appropriate warmth input. Excessive warm can bring about increased porosity as a result of the entrapment of gases in the weld pool. On the other hand, insufficient heat might cause insufficient fusion, developing possible powerlessness in the joint. Furthermore, utilizing the appropriate welding specifications, such as voltage, existing, and take a trip speed, is crucial for achieving audio welds with very little porosity.
Moreover, the selection of welding process, whether it be MIG, TIG, or stick welding, should align with the certain needs of the job to make certain ideal outcomes. Correct cleaning and preparation of the base metal, along with choosing the best filler product, are additionally vital parts of competent welding methods. By adhering to these best practices, welders can decrease the danger of porosity formation and create high-grade, structurally sound welds.
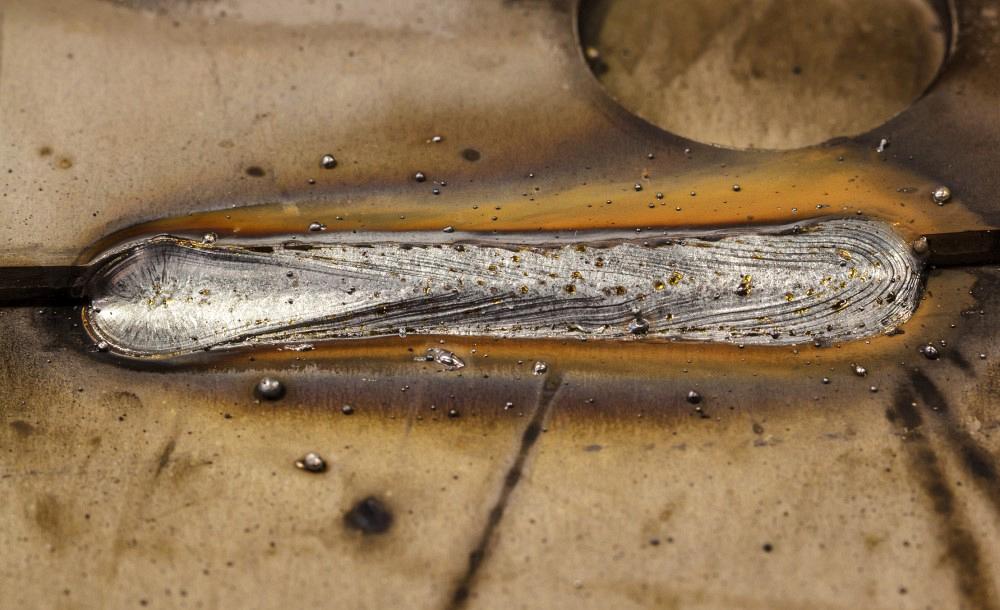
Testing and Quality Assurance Measures
Checking procedures are essential to spot and stop porosity in welding, guaranteeing the stamina and toughness of the last product. Non-destructive screening techniques such as ultrasonic screening, radiographic testing, and visual evaluation are typically employed to determine possible problems like porosity.
Post-weld assessments, on the other hand, evaluate the last weld for any type of flaws, consisting of porosity, and verify that it meets specified criteria. Applying a comprehensive quality control strategy that includes complete screening treatments and assessments is vital to lowering porosity problems and guaranteeing the total high quality of bonded joints.
Verdict
To conclude, porosity in welding can be a typical problem that affects the quality of welds. By recognizing the usual root causes of porosity and implementing best practices for prevention, such as appropriate welding strategies and testing measures, welders can guarantee high top quality and dependable welds. It is important to focus on avoidance approaches to minimize the incident of porosity and keep the stability of welded structures.